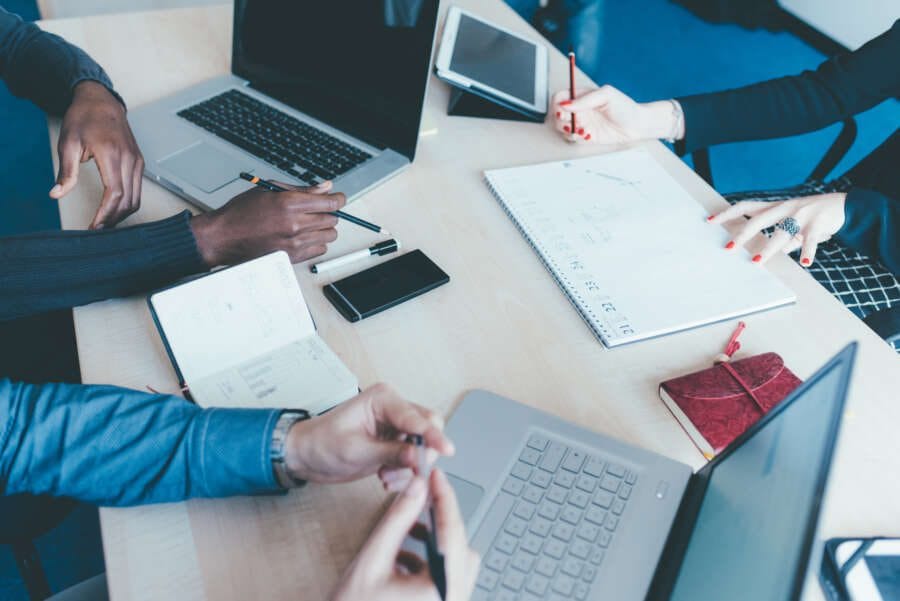
What is Operational Efficiency
What is Operational Efficiency
Operational efficiency refers to the capability of an organization to utilize its resources optimally to achieve its objectives while minimizing waste and costs. It involves streamlining processes, leveraging technology, and improving collaboration to enhance productivity and performance.
What is Efficiency in Business
Business efficiency refers to achieving the best possible results with minimal input, such as resources, time, or effort. It involves maximizing productivity, reducing waste, and maintaining quality to attain desired outcomes.
Importance of Operational Efficiency
- Effective Product Delivery: Operational efficiency streamlines processes, reducing delays and bottlenecks. This ensures products and services reach customers on time, enhancing satisfaction and building trust in the brand.
- Swift Response to Market Demands: Efficient operations enable businesses to adapt quickly to changing market conditions and customer preferences. This agility helps them seize opportunities and stay ahead of competitors.
- Competitive Advantage: Organizations with high operational efficiency can offer better prices, faster delivery, and superior customer service. This competitive advantage attracts more customers and strengthens their market position.
- Cost Reduction: By optimizing processes and resource allocation, operational efficiency lowers production costs and overhead expenses, leading to increased profitability.
- Resource Utilization: Efficient operations maximize the utilization of resources such as labor, materials, and equipment, minimizing waste and maximizing productivity.
- Improved Employee Morale: Smooth operations reduce frustration and stress among employees, boosting their morale and job satisfaction.
- Enhanced Customer Satisfaction: Efficient operations lead to better customer experiences, resulting in higher satisfaction levels, repeat business, and positive word-of-mouth referrals.
- Innovation and Growth: Operational efficiency frees up resources that can be redirected towards research, development, and innovation, fueling business growth.
- Risk Mitigation: A well-organized operational structure can identify and address potential risks promptly, reducing the likelihood of costly disruptions or failures.
- Sustainable Growth: Sustaining operational efficiency fosters long-term growth, allowing businesses to adapt to changes and challenges in the industry and economic environment.
Key Metrics and Indicators of Operational Efficiency
Various metrics and indicators help measure operational efficiency, such as
- Throughput: Throughput measures the rate at which a system or process can produce outputs in a given time frame. It indicates the efficiency of production or service delivery and is essential for optimizing resource utilization and meeting customer demand.
- Cycle Time: Cycle time refers to the time taken to complete one cycle of a process, from start to finish. Reducing cycle time enhances operational efficiency by speeding up production or service delivery, allowing businesses to be more responsive to market demands.
- Capacity Utilization: Capacity utilization measures the extent to which available resources, such as machines, equipment, or labor, are being utilized in production or service delivery. High capacity utilization indicates efficient resource management and cost-effectiveness.
- Customer Satisfaction: Customer satisfaction gauges how well a business meets customer expectations and requirements. Satisfied customers are more likely to become loyal and recommend the business to others, contributing to long-term success.
- Employee Productivity: Employee productivity measures the output or value of work produced by employees over a specific period. High employee productivity indicates an engaged and efficient workforce, leading to better operational performance..
Factors Affecting Operational Efficiency
A. Process Optimization
Streamlining and optimizing business processes are essential for operational efficiency. Businesses must regularly review and re-engineer their workflows to eliminate inefficiencies and adapt to changing demands.
B. Resource Management
- Human Resources: Effective utilization of the workforce is crucial for operational efficiency. Proper training, skill development, and workload distribution contribute to increased productivity and reduced turnover.
- Financial Resources: Financial management plays a pivotal role in ensuring operational efficiency. Budget allocation, cost control, and smart investments lead to sustainable growth.
- Physical Resources: Optimizing the use of physical assets, such as machinery and equipment, helps reduce downtime and maintenance costs, contributing to operational efficiency.
C. Technology and Automation
Leveraging technology and automation can significantly enhance operational efficiency. Integrating advanced software and robotics in manufacturing, customer support, and other areas improves accuracy and speed.
D. Communication and Collaboration
Efficient communication and collaboration between teams and departments promote seamless operations. Encouraging transparency and information sharing fosters a unified organizational culture.
Benefits of Improving Operational Efficiency
- Cost Reduction: Operational efficiency leads to cost savings through reduced waste, increased productivity, and optimized resource utilization. This allows businesses to allocate funds strategically for growth initiatives.
- Increased Productivity:Enhanced processes and resource management result in increased productivity, enabling businesses to deliver more output in less time.
- Enhanced Customer Satisfaction: Operational efficiency positively impacts customer satisfaction as it ensures timely delivery of products and services, improved quality, and better customer support.
- Competitive Advantage: Operational efficiency can become a differentiating factor in a competitive market, helping businesses attract more customers and gain a sustainable advantage over rivals.
Strategies to Achieve Operational Efficiency
- Lean Principles and Practices: Adopting lean principles, such as Just-In-Time (JIT) inventory management and reducing waste through continuous improvement, can enhance operational efficiency significantly.
- Six Sigma Methodology: The Six Sigma methodology aims to minimize defects and variations in processes, leading to increased efficiency and improved product quality.
- Total Quality Management (TQM): TQM involves a holistic approach to quality improvement, where all employees participate in enhancing processes, thereby contributing to operational efficiency.
- Business Proess Reengineering (BPR): BPR involves radical redesign and reorganization of business processes to achieve substantial efficiency improvements and fundamental changes in performance.
- Continuous Improvement: Encouraging a culture of continuous improvement ensures that businesses remain proactive in seeking better ways to optimize processes and operations.
Challenges in Achieving Operational Efficiency
- Resistance to Change: Resistance to change from employees and management can hinder the implementation of operational efficiency strategies.
- Lack of Data and Insights: Insufficient data and insights can impede the accurate assessment of operational performance and hinder the identification of improvement opportunities.
- Inefficient Processes and Systems: Outdated or inefficient processes and systems can create bottlenecks and hinder operational efficiency.
- Organizational Silos: Lack of collaboration and communication between different departments can lead to information silos, limiting operational efficiency.
Tools and Technologies for Enhancing Operational Efficiency
- Enterprise Resource Planning (ERP) Systems: ERP systems integrate various business processes and functions, streamlining operations and facilitating data-driven decision-making.
- Business Process Management (BPM) Software: BPM software helps organizations model, automate, and optimize processes, leading to increased efficiency and agility.
- Data Analytics and Business Intelligence: Data analytics and business intelligence tools provide valuable insights into operational performance, enabling businesses to make informed decisions.
- Robotic Process Automation (RPA): RPA automates repetitive tasks, reducing errors and freeing up employees to focus on more strategic activities.
Measuring and Monitoring Operational Efficiency
- Key Performance Indicators (KPIs): KPIs help track and measure the performance of various processes, providing insights into operational efficiency.
- Benchmarking: Benchmarking involves comparing performance metrics against industry best practices to identify areas for improvement.
- Performance Reviews and Assessments: Regular performance reviews and assessments allow businesses to identify successes and shortcomings in their operational efficiency efforts.
In conclusion, operational efficiency is vital for success. Optimize processes, embrace technology, and foster collaboration to reduce costs, improve productivity, and satisfy customers. Continually adapt to changing trends and best practices for ongoing improvement. Implement strategies for operational excellence, customer-centricity, and employee engagement to stay competitive and achieve sustainable growth.